The pillar drill
The pillar drill is one of the most useful stationary machines in a workshop. You can find information about their multitude of applications here!Thus, not only the accuracy of the drilling is highlighted, but in particular the versatility of applications. But what should you look for when buying such a machine and what can you do with it, other than simply drilling? I will explain the most important factors to consider when making a purchase. I will also show you how build a large drill table with stop yourself.
What can you drill with a pillar drill?
Of course, a drill drills holes. But would you have thought that you could turn a pillar drill into a stationary spindle grinder, or saw or polish holes with it? You can even remove rust from metal parts with a round wire brush. I will show show you later how to do so!
Using a pillar drill, standard drilling is not only quicker, but also more precise than with a hand‐held drill. With some models, the drill table can not only be moved up and down, but even in different angles (radially). With some home‐made accessories there are a variety of different processing options.
But let’s start at the beginning.
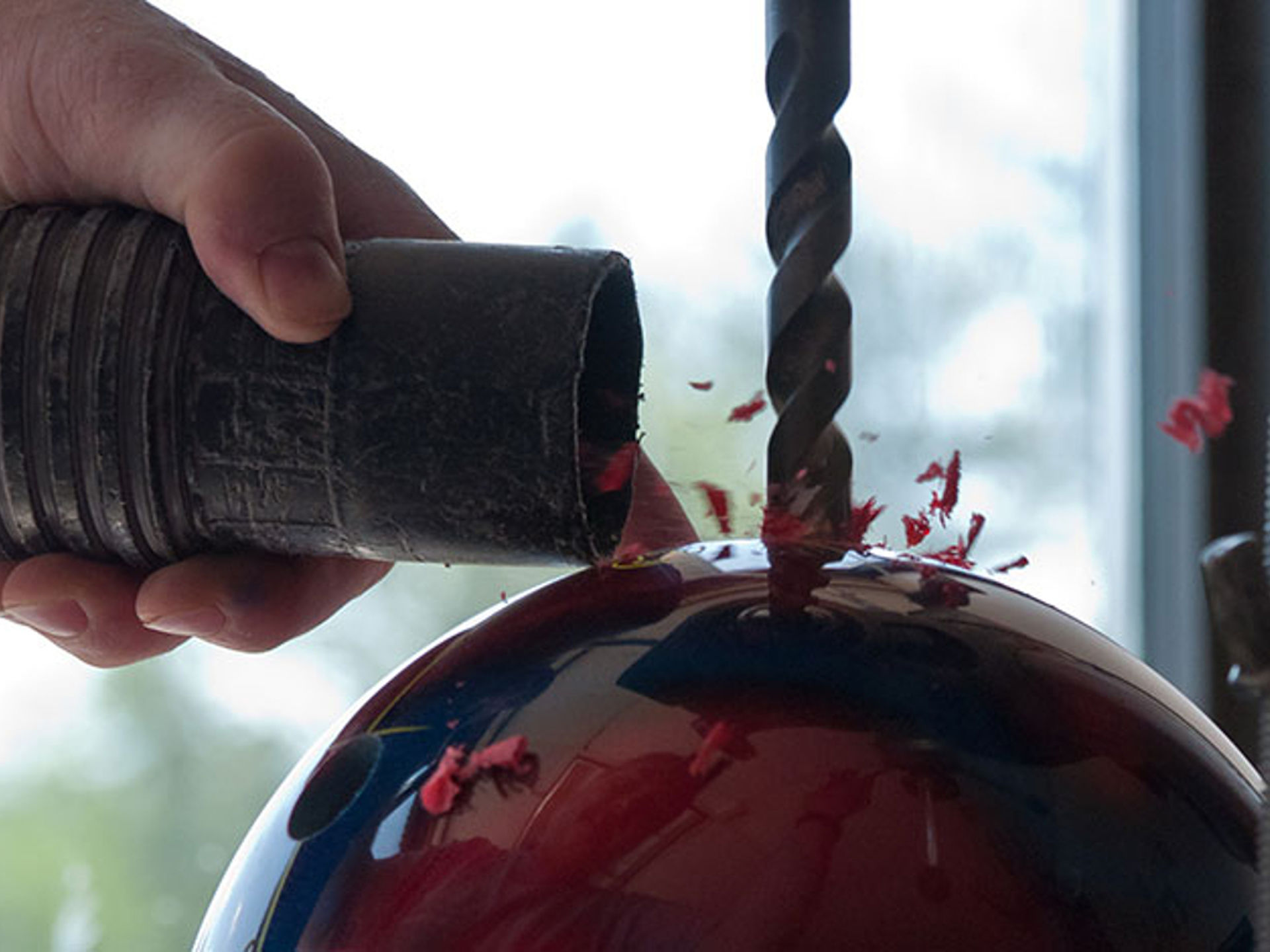
What should you look out for when making a purchase?
As with almost all tools, the purpose is decisive. The size of the work piece to be processed, as well as the question of its material are decisive factors that should be considered when making a purchase. However, if you’re more of a model maker, you do not need a 1.6 m tall, 700 watt drill with 24 rpm and 400 volt connection, but rather the smaller version. DIYers who work with both wood and metal and want to pierce a 5 mm flat iron but also sometimes a 100 mm wooden beam, should opt for a drill with sufficient power and a reasonable chuck.
Speed regulation and performance
Most pillar drills have speed regulation which is controlled by different stepped belt pulleys and with the appropriate V‐belt. A proven system, which is in a higher price category, upgraded with a stepless digital control. The smaller the drill, the higher the speed should be. In case you want to cut a thread, it is also important to have low speed. A constant speed heavily relies on the power of the motor. The higher the power, the more uniform the speed. Speeds of 120–2,500 rpm are standard and sufficient for DIY applications. The power should be between 350 and 700 watts.
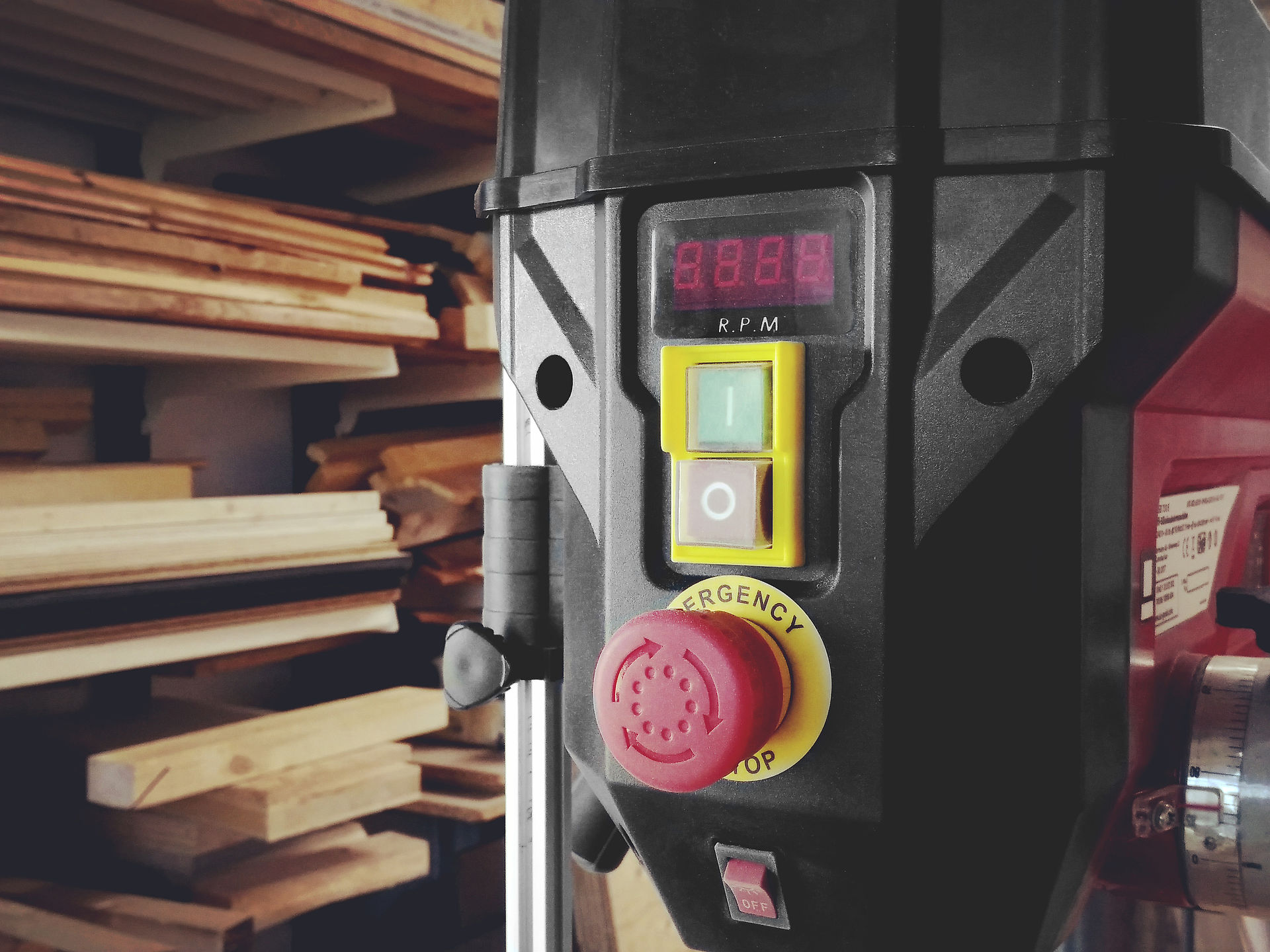
Drill mount
The mount for the drill is offered as a scroll chuck or better with a quick release chuck. You don’t need a drill foot key with a quick release chuck. The size of the mount is important. With larger drill chucks these usually only start at 1.5 mm and are therefore out of the question for passionate model makers. The maximum mount size of 16 mm leaves the allrounder enough play for special applications. If the drill still has a cone mount (e. g. MK2), you can swap the chuck for another one.
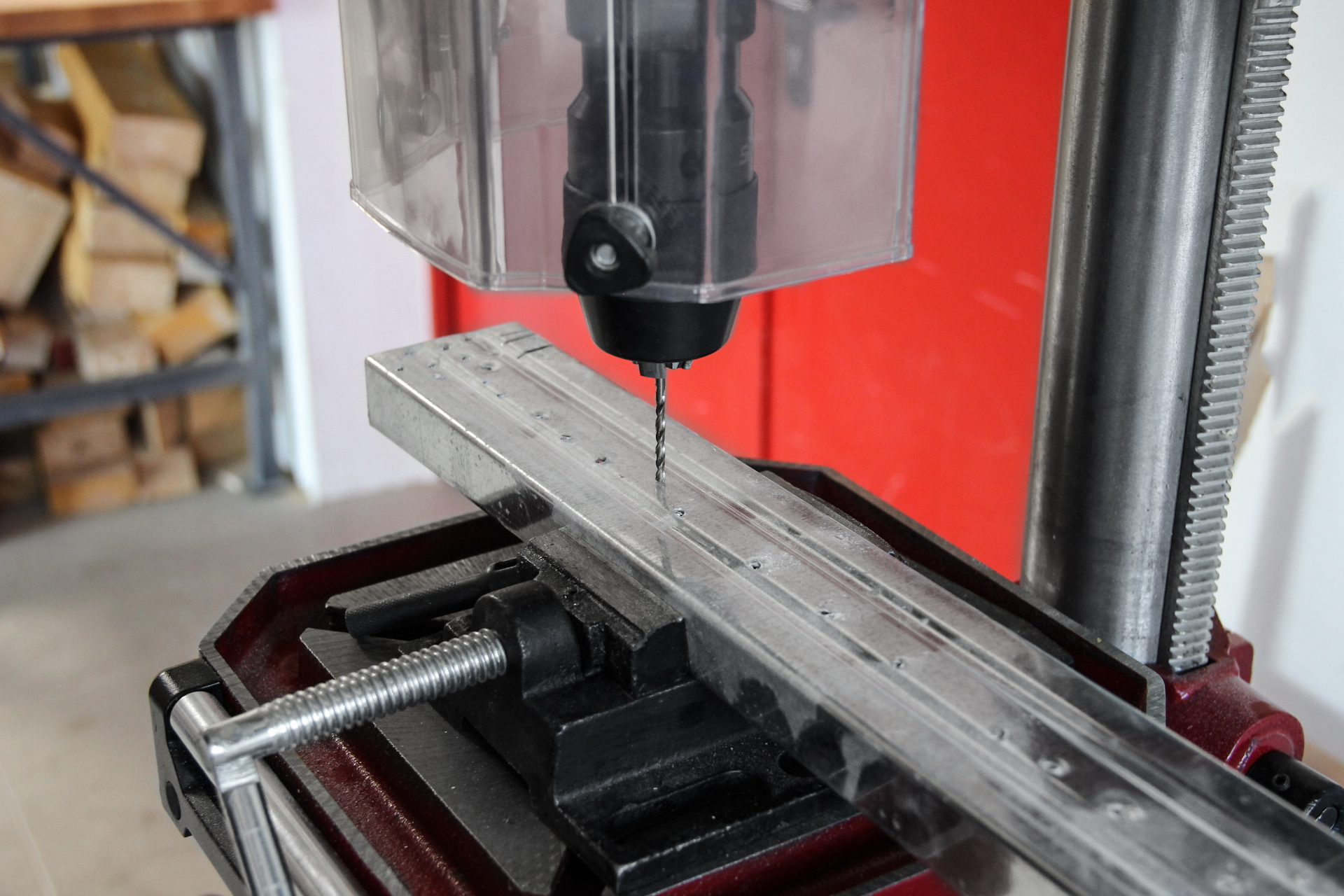
Other functions
The main area of application is metal working, because precision matters more here. This can be seen in the usually relatively small drill table, which in addition to slots for fixing machine vices is also provided with a groove for cooling liquid. If you want to cut threads with the machine, a right/left rotation switch is important. The drilling depth is of course important if you want to drill large parts. It is usually between 50 and 80 mm.
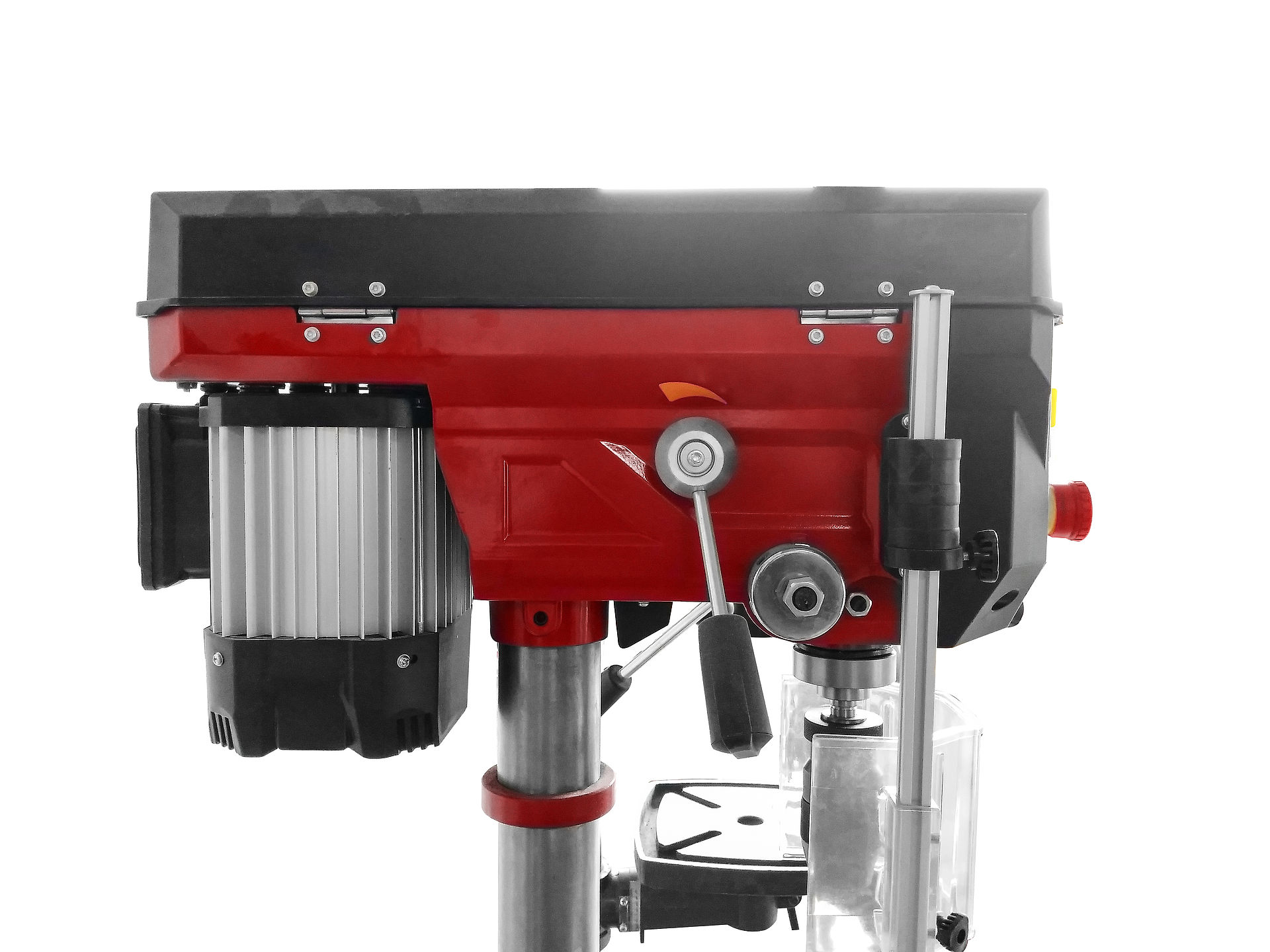
Other advantages of a pillar drill
A pillar drill is particularly suited for larger holes with Forstner drills or a hole saw. By hand, this is really exhausting and uneven. Furthermore, the drill bits do not break off so quickly during metalworking because in contrast to hand‐held drills, they strike the workpiece exactly straight. In addition, you can use it to build up a greater pressure while drilling. It is also a significant advantage if the machine is equipped with a depth limit. If you want to drill holes for wooden dowels, for example, this device will help you enormously because the holes will all be the same depth.
There are many accessories for the pillar drill, but in my opinion the most useful accessory is the drill table. In most cases this is a little too small. Therefore, I have built an additional drill table that is fitted with a longitudinal stop. This allows me to drill holes in series without always having to measure again. For example, with a bar that is to be provided with booms or a long board, which must be pre‐drilled for screwing.
The simplest variant is a slightly thicker, smooth board (e. g. 25 mm multiplex), into which you saw two slots (10 mm) (see drawing). A straight bar (e. g., 44x44 mm spruce) serves as a stop and is provided with two through holes. Through the bar you plug, carriage bolts (for example) long enough to secure the bar and board down with washers and wing nuts. Then you screw the board to the existing drill table. Now you have an extended mount and can make drilling in series easier. Boards and larger workpieces rest securely on the mount and simplify drilling.
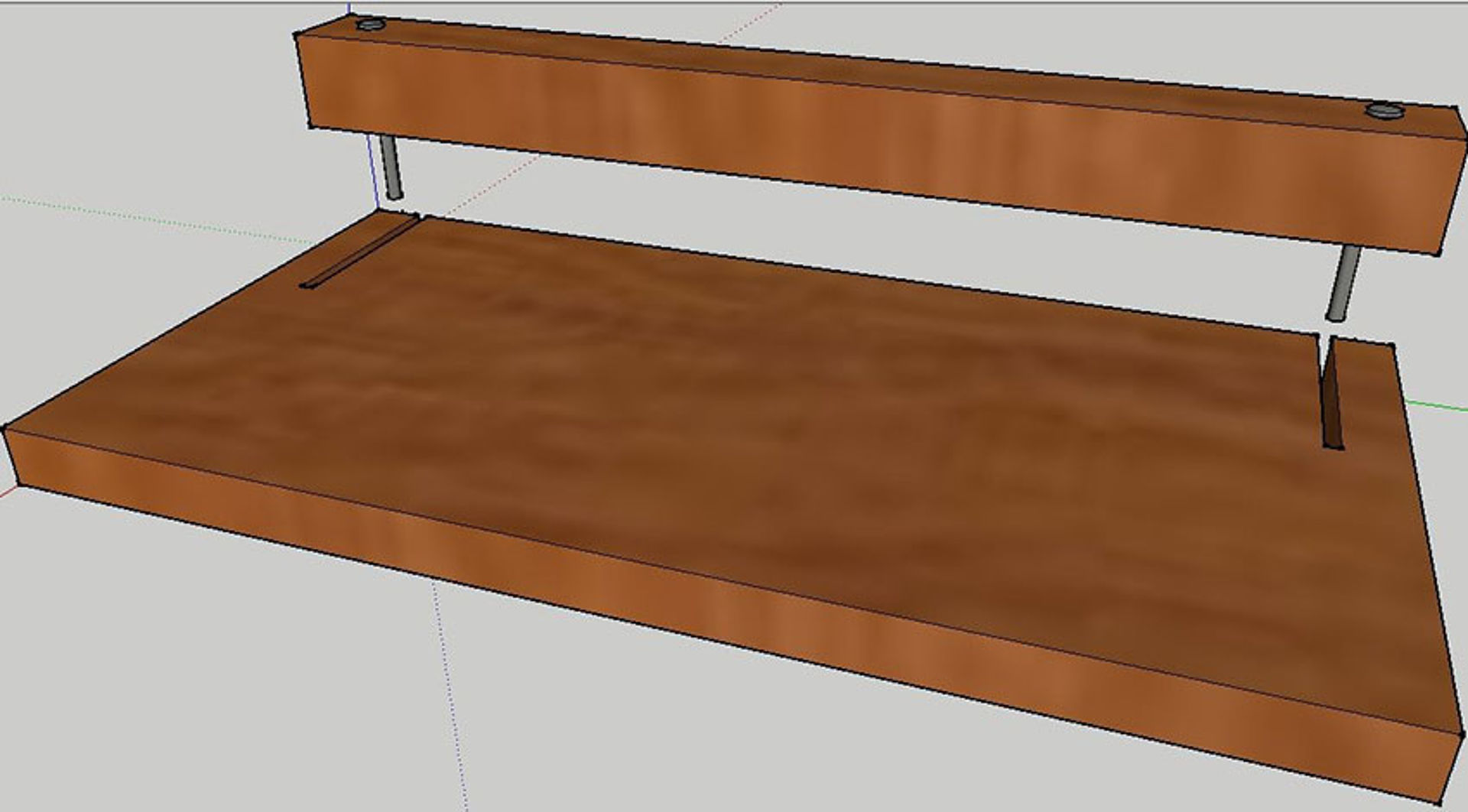
Another Variant
I have doubled the mount width, the middle part of the upper board being interchangeable in case I have drilled through too many times. The guide of the stop also runs over the entire width of the table, as I have milled a groove under the top board. To do this, you mill two slots in the lower board before gluing the two boards (for me that was 18 mm wide and about 10 mm deep). Now you glue the top board to the bottom board and after the glue has set, mill a smaller but continuous groove (for me, 6 mm) in the top board. You only have to consider the middle of the lower grooves. Now you can insert a carriage bolt with the head in the groove and screw on top of the stop wing nuts to tighten.
I hope I could enlighten you about the advantages of a stationary pillar drill. I use it often and wouldn't want to be without it. To step out of the ordinary I am going to show you how to pimp your stationary drill.
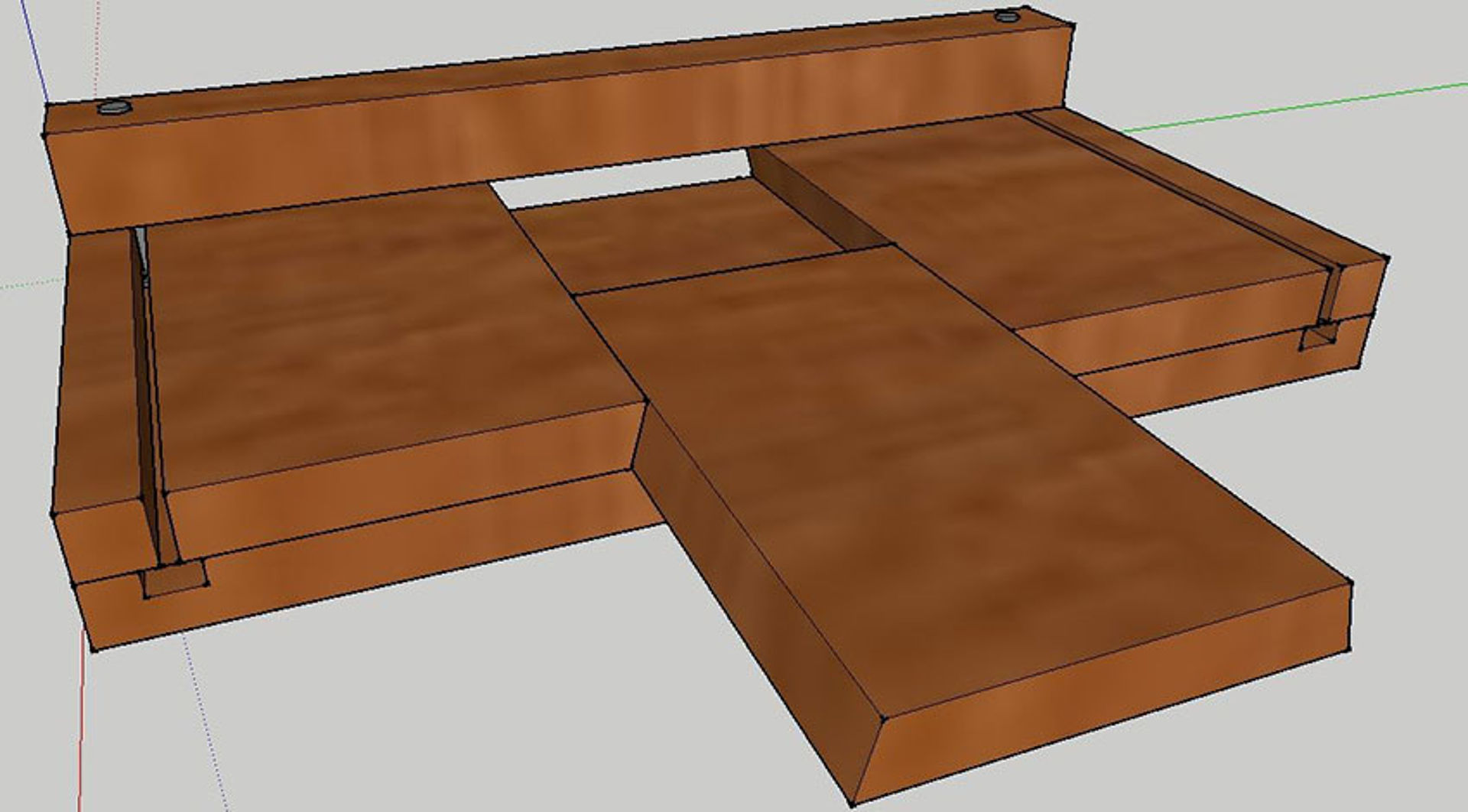
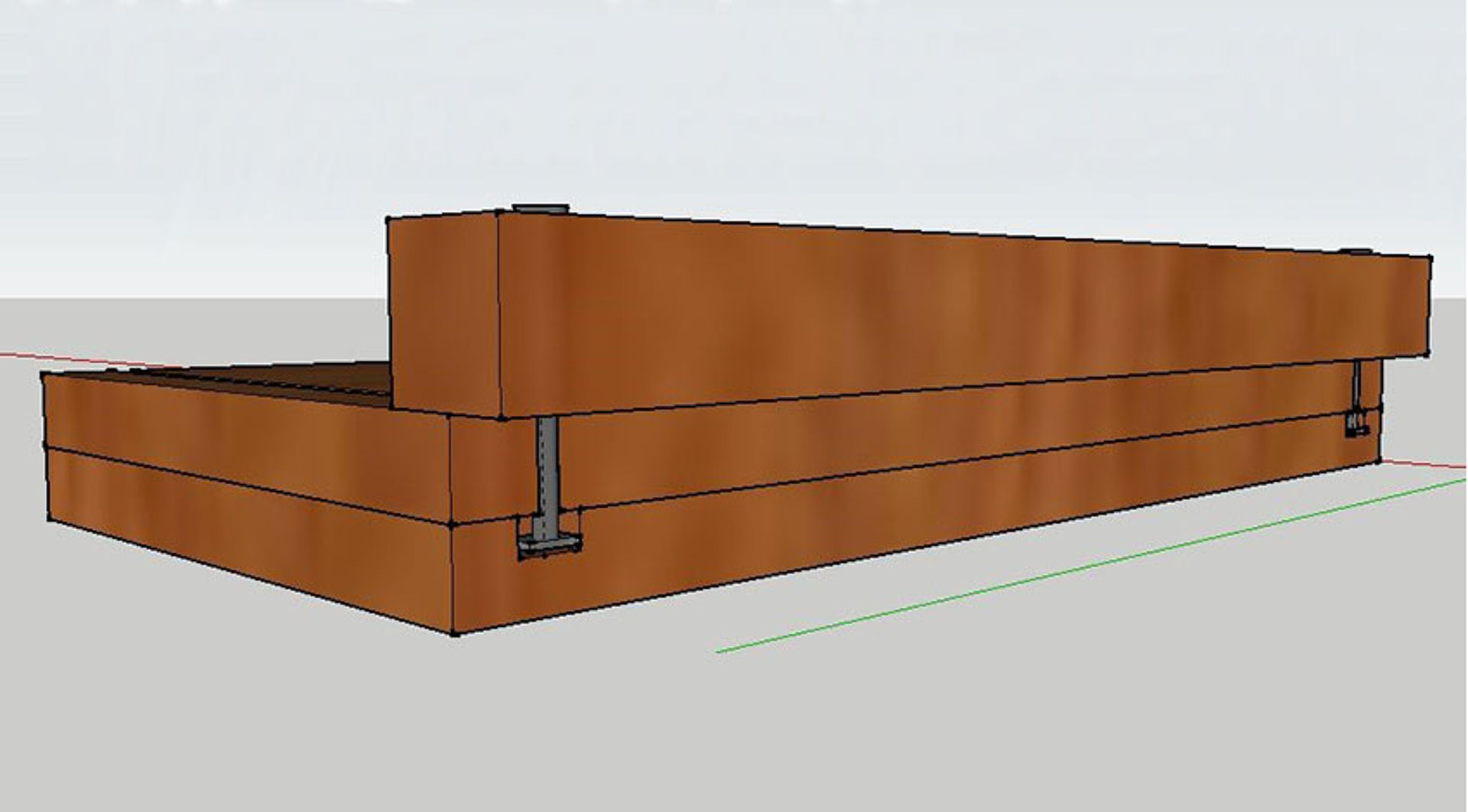
How to expand it into a spindle grinder!
A spindle grinder is always very useful if you want to work on inner radii and other tools do not work best here. The inner radii are machined with sanding rollers of different sizes. You can buy them or you can make them the same size as you need them. Wood residues from a multiplex board are best suited for this purpose. You saw off circular discs to the desired diameter with a hole saw.
The amount depends on the desired height of the roller. My rollers are approx. 12.5 cm tall, with 25 mm multiplex, so 5 discs. They are each coated with glue on one surface.
Now place the discs on a threaded rod with the diameter of the centre drill of the hole saw and squeeze them together with a nut and large washers until the glue has set.
Stretch the resulting roller in the drill press. In order to make the surface flat, glue half a sheet of sandpaper (80 grit) onto a smooth board using glue or spray glue. Now when you start the drill, you can slowly hold the sandpaper to the outside of the roller and work the surface until it is smooth and even.
Then saw with a hacksaw or a tenon saw, carefully sawing a 1 cm deep slit in the roll.
This is a bit fiddly the first time, but it works. So that the sanding paper cannot slip out during operation, place a nail into the slot at the top and bottom and secure it there. Your sanding roller is now ready and you can produce it in different sizes. The principle always remains the same.
Now, when sanding with this kind of sanding roller, a lot of sanding dust is created. It is also cheaper if you can use a mount surface that is at right angles to the grinding wheel. For this, we will now build a work table with connection options for your workshop vacuum cleaner.
This is a 10 cm tall closed box, into which the sanding roller dips. The dust is vacuumed up through a hole (35 mm diameter) in the side.
It is very important to me in the everyday life of DIY, that the construction is always quick. Therefore, the box is designed so that it can be attached to my existing drill table with screw clamps.
The base and cover plates are the same size as the drill table: 700 mm wide and 250 mm deep. The box into which the sanding roller dips does not need to be as big (300x250 mm).
As I have sanding rollers in different sizes, the hole must correspond to the respective size. This works best with inserts that can be exchanged. For this purpose I sawed a quadrangular cutout with a jigsaw and screwed down two flat irons with an overhang. Then I can place the inserts that I made from the same plate as the cover plate. Thus, I ensure that everything is flat. For the insert you saw a 150x150 mm plate. The hole in the inserts should have a diameter approx. 2–3 mm greater than the respective sanding roller. I have worked on the surface of the inserts with my multi grinder so that they sit properly and the workpiece does not get stuck anywhere. You can screw a long screw into the sides to hold different inserts. Finally, I treated the surfaces of the cover plate and the inserts with wax (e. g. antique wax) to better guide the workpiece.
Now your work table and spindle grinder are ready!