Die Säulenbohrmaschine
Die Säulenbohrmaschine gehört zu den nützlichsten stationären Maschinen in einer Werkstatt. Informationen zur Vielseitigkeit der Anwendung finden Sie hier!Dabei ist nicht nur die Genauigkeit der Bohrungen hervorzuheben, sondern vor allem die Vielseitigkeit der Anwendungsmöglichkeiten. Doch worauf sollte ich beim Kauf einer solchen Maschine achten und was kann ich noch damit machen, außer dem reinen Bohren? Ich erkläre dir die wichtigsten Faktoren, die für den Kauf entscheidend sind. Weiterhin zeige ich dir, wie man einen größeren Bohrtisch mit Anschlag selber baut.
Was kann eine Säulenbohrmaschine?
Klar, mit einer Bohrmaschine bohrt man Löcher. Hättest du aber gedacht, dass man aus einer Säulenbohrmaschine eine stationäre Spindelschleifmaschine machen kann, mit ihr Löcher sägen oder polieren kann? Du kannst sogar Metallteile mit einer Runddrahtbürste entrosten.
Das klassische Bohren gelingt mit einer Säulenbohrmaschine nicht nur schneller, sondern wesentlich exakter, als mit einer handgeführten Bohrmaschine. Bei einigen Modellen lässt sich der Bohrtisch nicht nur hoch und runter, sondern sogar in verschiedene Winkel (radial) verstellen. Mit ein paar selbstgebauten Zubehörteilen, ergeben sich eine Vielzahl von unterschiedlichen Bearbeitungsmöglichkeiten.
Aber fangen wir von vorne an.
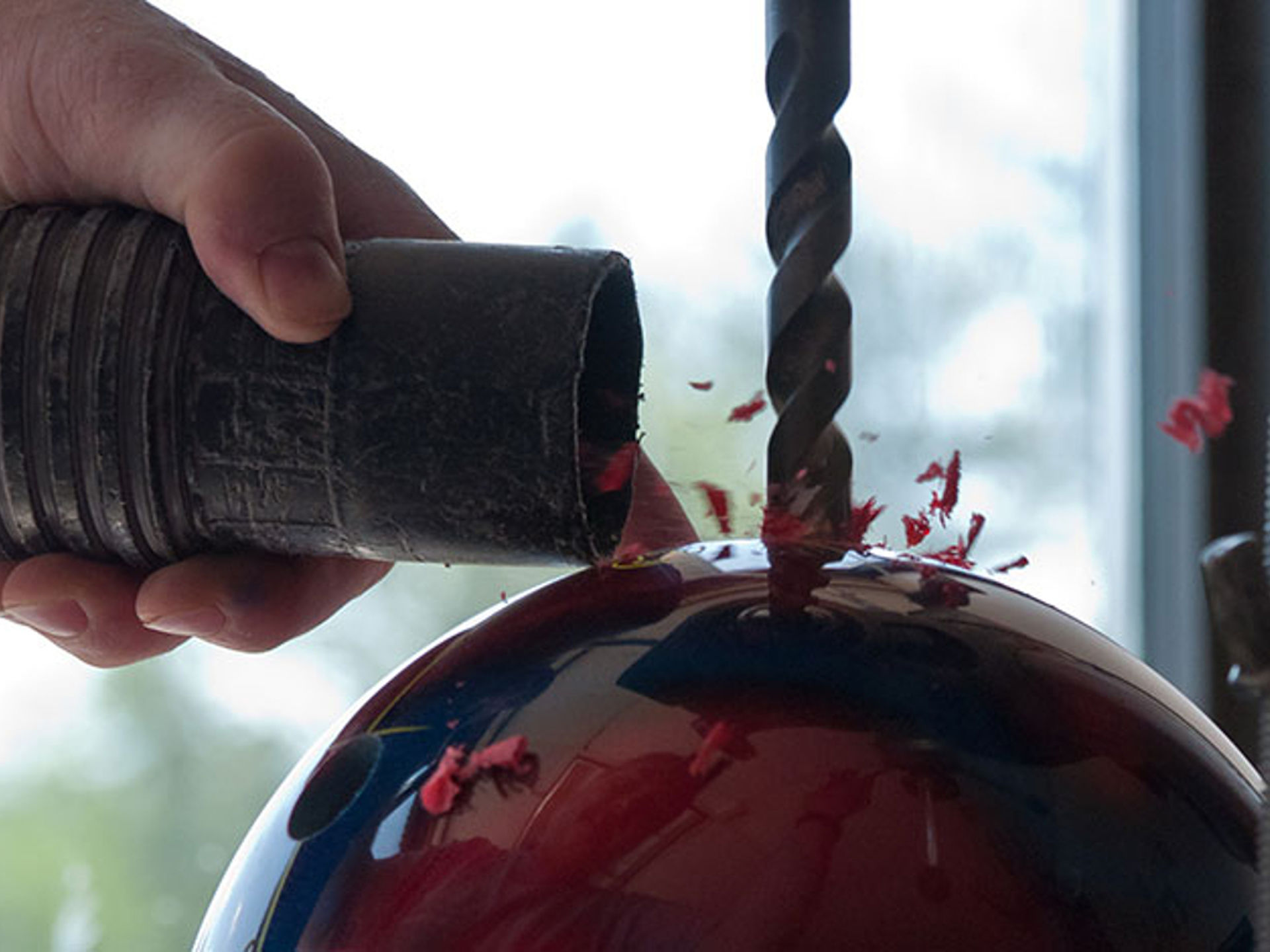
Worauf solltest du beim Kauf achten?
Wie bei fast allen Werkzeugen ist der Verwendungszweck entscheidend. Die Größe der zu bearbeitenden Werkstücke, sowie die Frage nach dem jeweiligen Werkstoff sind entscheidende Faktoren, die es beim Kauf zu berücksichtigen gilt. Wenn du eher der Modellbauer bist, brauchst du keine 1,6 m hohe und 700 Watt starke Bohrmaschine mit 24 Drehzahlstufen und 400 Volt Anschluss, sondern eher die kleinere Variante. Der Heimwerker, der sowohl Holz, als auch Metall bearbeitet, mal ein 5 mm Flacheisen aber auch manchmal den 100er Holzbalken durchbohren will, sollte sich für eine Bohrmaschine mit ausreichend Leistung und einem vernünftigen Bohrfutter entscheiden.
Drehzahlregulierung und Leistung
Viele Säulenbohrmaschinen haben eine Drehzahlregulierung, die über unterschiedliche Stufen‐Riemenscheiben und mit dem entsprechenden Umlegen eines Keilriemens geregelt wird. Ein bewährtes System, das in einer höheren Preiskategorie liegt, wird durch eine stufenlose digitale Steuerung aufgewertet. Je kleiner der Bohrer, desto höher sollte die Drehzahl sein. Für den Fall, dass du Gewinde schneiden willst, ist wiederum eine niedrige Drehzahl wichtig. Dabei hängt eine konstante Drehzahl von der Leistung des Motors ab. Je höher die Leistung, desto gleichmäßiger die Drehzahl. Drehzahlen von 120 – 2500 Umdr./Min sind Standard und für die heimwerkliche Anwendung ausreichend. Die Leistung sollte zwischen 350 und 700 Watt liegen.
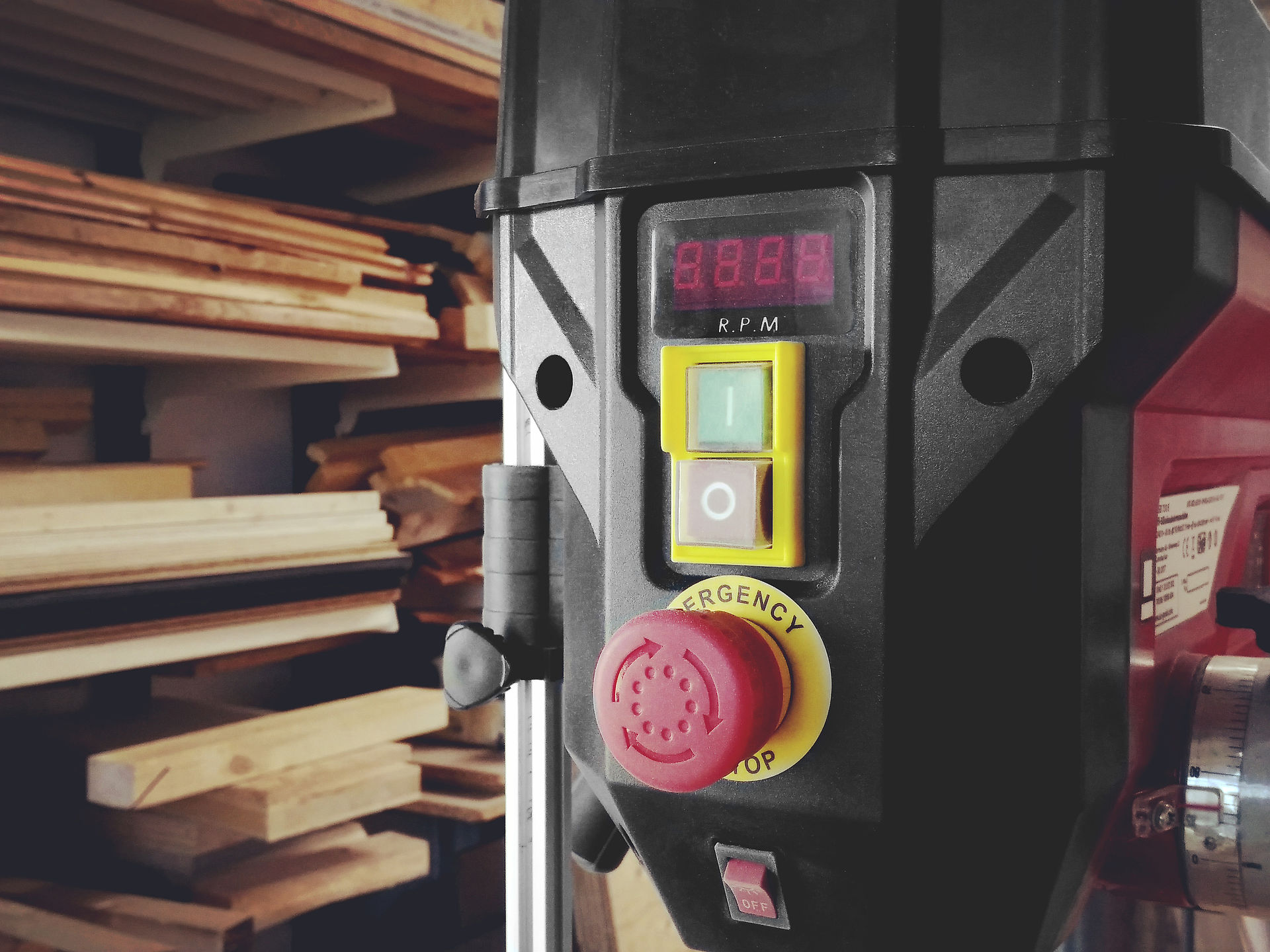
Bohreraufnahme
Die Aufnahme für die Bohrer wird als Zahnkranzfutter oder besser mit einem Schnellspann‐Bohrfutter angeboten. Beim Schnellspann‐Bohrfutter benötigst du keinen Bohrfutterschlüssel. Wichtig ist dabei die Größe der Aufnahme. Bei größeren Bohrfuttern gehen diese meistens erst ab 1,5 mm los und kommen somit für den passionierten Modellbauer nicht in Frage. Die Maximalaufnahme von 16 mm lässt für den Allrounder dabei genug Spielraum für besondere Aufgaben. Hat die Maschine dann noch eine Kegelaufnahme (z. B. MK2), kannst du das Bohrfutter gegen ein anderes tauschen.
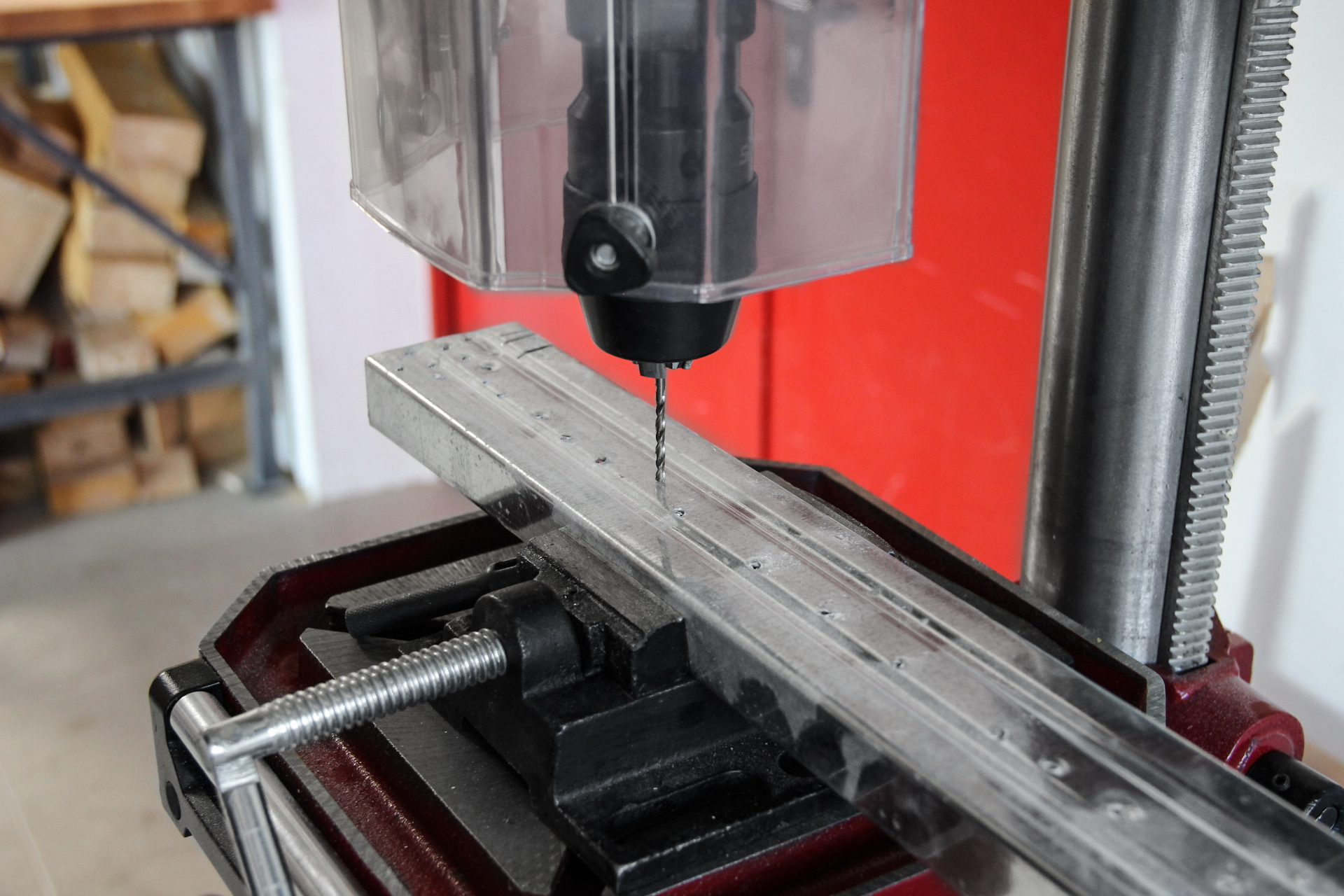
Weitere Funktionen
Der Haupteinsatzbereich ist die Metallbearbeitung, weil es hier eher auf Präzision ankommt. Das erkennt man an dem üblicherweise relativ kleinen Bohrtisch, der neben Schlitzen für das Fixieren von Maschinenschraubstöcken auch mit einer Auffangrinne für Kühlflüssigkeit versehen ist. Wenn du mit der Maschine vielleicht sogar Gewinde schneiden willst, ist eine Rechts‐/Linkslauf‐Umschaltung wichtig. Die Bohrtiefe ist natürlich immer dann wichtig, wenn du große Teile bohren willst. Sie liegt üblicherweise zwischen 50–80 mm.
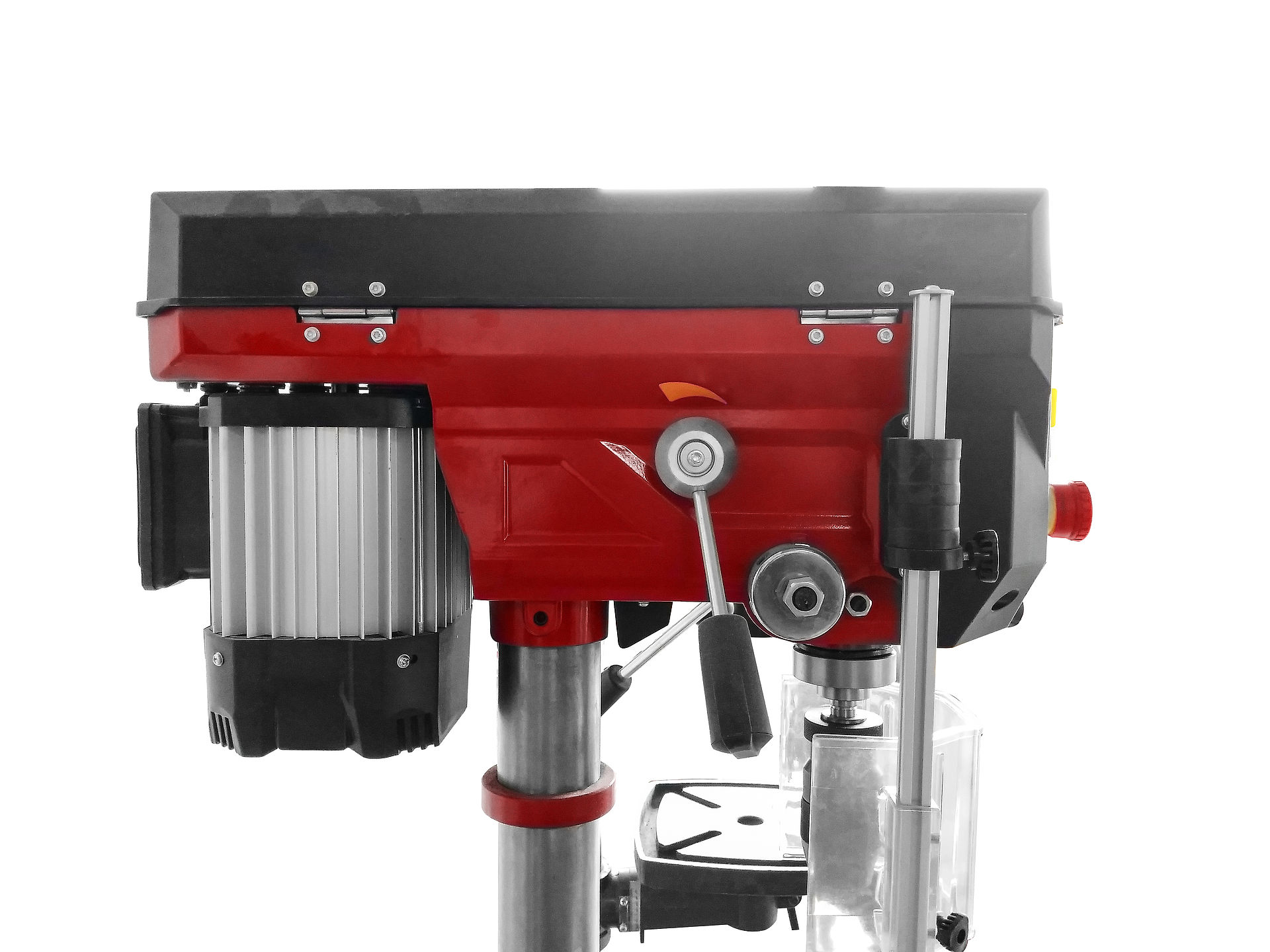
Weitere Vorteile einer Säulenbohrmaschine
Eine Säulenbohrmaschine eignet sich hervorragend um größere Löcher mit Forstnerbohrern oder einer Lochsäge herzustellen. Von Hand ist das wirklich sehr anstrengend und ungenau. Weiterhin brechen die Bohrer bei Metallbearbeitung nicht so schnell ab, weil sie im Gegensatz zu handgeführten Bohrmaschinen genau gerade auf das Werkstück treffen. Außerdem kannst du damit einen größeren Druck beim Bohren aufbauen. Von großem Vorteil ist es auch, wenn die Maschine mit einer Tiefenbegrenzung ausgestattet ist. Für den Fall, dass du z. B. Löcher für Holzdübel bohren willst, hilft dir diese Einrichtung enorm, weil die Löcher alle gleich tief sind.
Es gibt viel Zubehör für die Säulenbohrmaschine, aber das meiner Meinung nach nützlichste Zubehör ist der Bohrtisch. In den meisten Fällen fällt dieser etwas zu klein aus. Ich habe mir deshalb einen zusätzlichen Bohrtisch gebaut, der mit einem Längsanschlag ausgestattet ist. Damit kann ich Löcher in Serie bohren, ohne immer neu messen zu müssen. Beispielsweise bei einer Leiste, die mit Holdübeln versehen werden soll oder bei einem langen Brett, das zum Schrauben vorgebohrt werden muss.
Die einfachste Variante ist ein etwas stärkeres, glattes Brett (z. B. 25 mm Multiplex), in das du zwei Schlitze (10 mm) sägst (siehe Zeichnung). Eine gerade Leiste (z. B. 44x44mm Fichte) dient als Anschlag und wird mit zwei Durchgangsbohrungen versehen. Durch die Leiste steckst du z. B. Schlossschrauben, die lang genug sind, um die Leiste und das Brett unten mit Unterlegscheiben und Flügelmuttern festschrauben zu können. Im Anschluss schraubst du das Brett an den vorhandenen Bohrtisch. Nun hast du eine vergrößerte Auflage und kannst Serienbohrungen einfacher herstellen. Bretter und größere Werkstücke liegen sicher auf der Auflage und vereinfachen das Bohren.
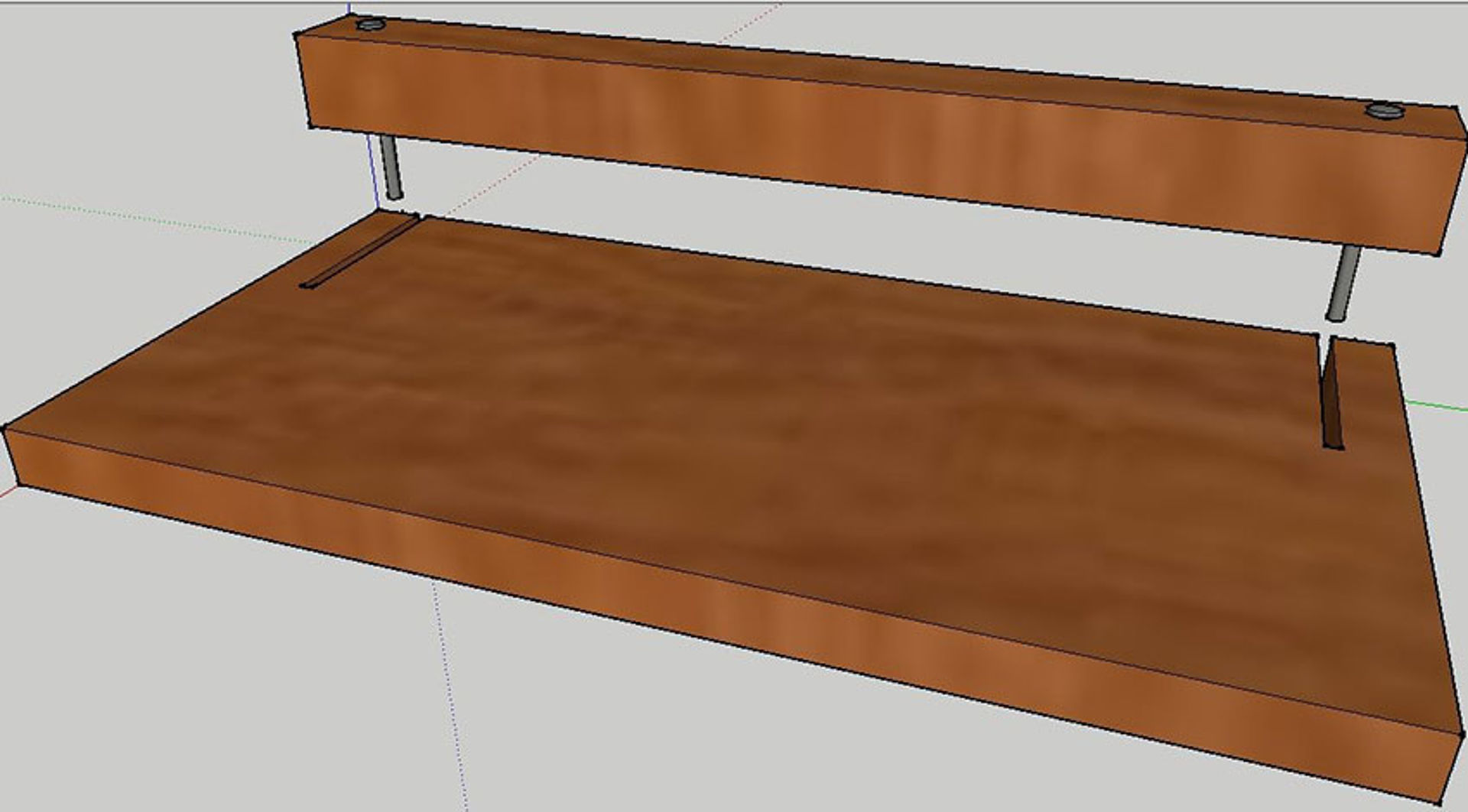
Eine weitere Variante
Ich habe das Auflagebrett gedoppelt, wobei der Mittelteil des oberen Brettes austauschbar ist, für den Fall, dass ich zu oft durchgebohrt habe. Die Führung des Anschlages verläuft zusätzlich über die gesamte Breite des Tisches, weil ich unter dem oberen Brett eine Nut eingefräst habe. Dazu fräst du vor dem Verleimen der beiden Bretter in das untere Brett zwei Nuten ein (bei mir war das 18 mm breit und etwa 10 mm tief). Nun verleimst du das obere mit dem unteren Brett und fräst nach dem der Leim abgebunden hat eine kleinere, aber durchgehende Nut (bei mir 6 mm) in das obere Brett. Du musst nur die Mitte der unteren Nut berücksichtigen. Jetzt kannst du eine Schlossschraube mit dem Kopf in der Nut führen und oben auf dem Anschlag Flügelmuttern zum Festziehen aufschrauben.
Ich hoffe ich konnte dir die Vorzüge einer stationären Säulenbohrmaschine etwas näher bringen. Ich benutze sie sehr oft und möchte auch nicht auf sie verzichten. Um nun das Alltägliche zu verlassen, zeige ich euch wie ihr eure Säulenbohrmaschine pimpen könnt!
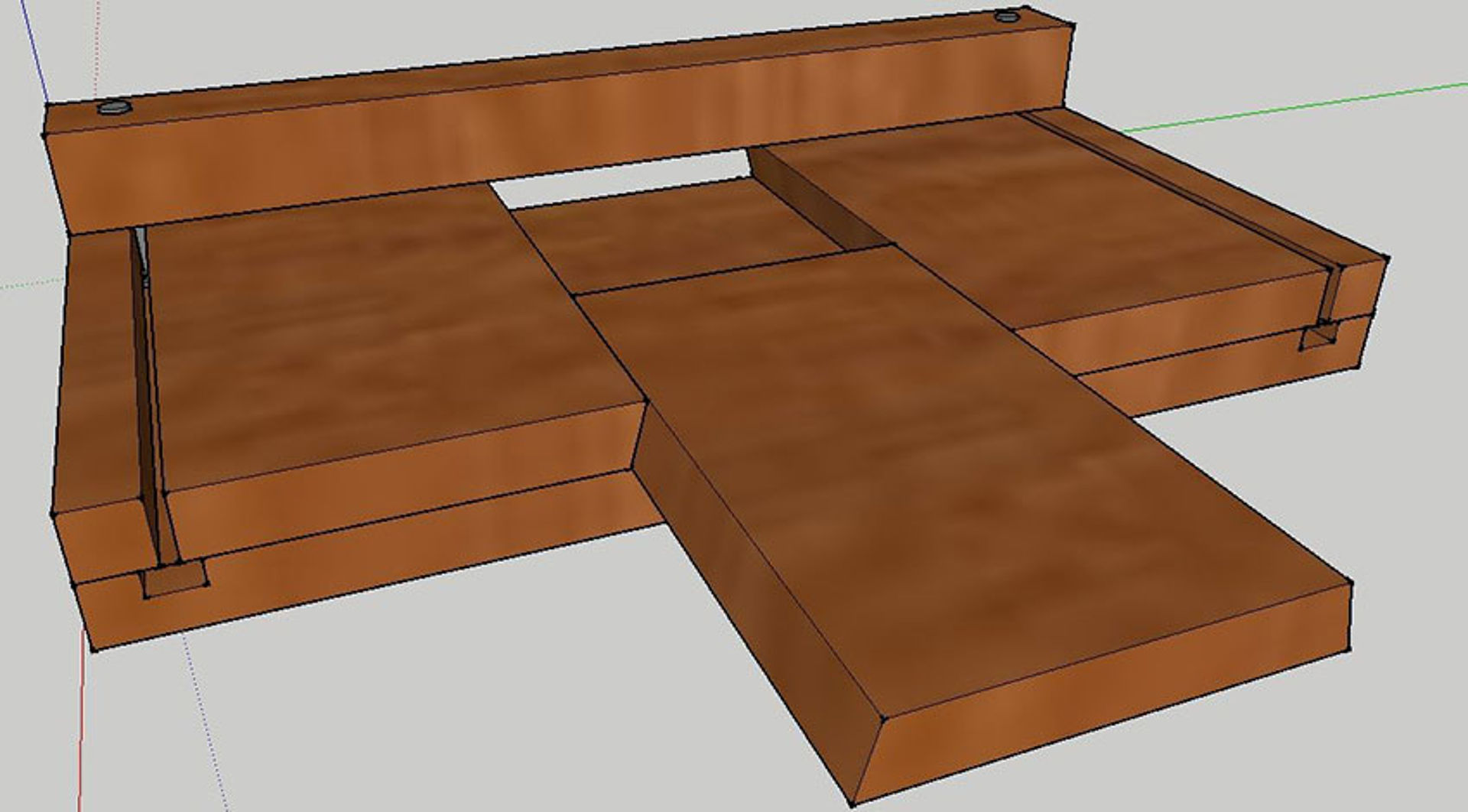
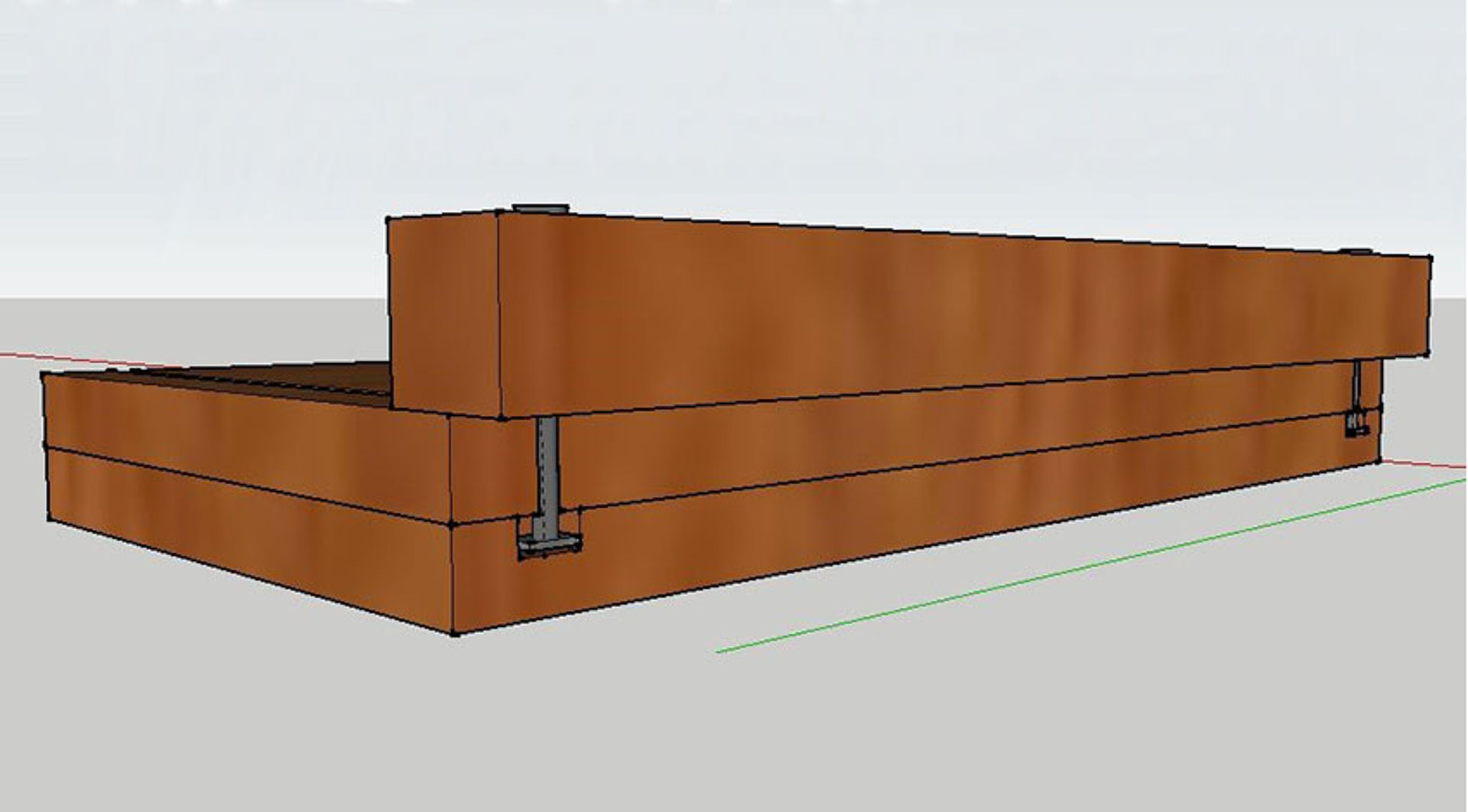
Wir erweitern sie zur Spindelschleifmaschine!
Ein Spindelschleifer ist immer dann sehr nützlich, wenn du Innenradien bearbeiten möchtest und andere Werkzeuge hier nicht optimal arbeiten können. Die Innenradien werden mit Schleifwalzen in unterschiedlichen Größen bearbeitet. Diese kann man kaufen oder du machst sie besser gleich selbst in genau der Größe, wie du sie benötigst. Am besten eignen sich dafür Holzreste aus einer Multiplexplatte. Mit einer Lochsäge sägst du kreisrunde Scheiben in dem gewünschten Durchmesser aus.
Die Anzahl hängt von der gewünschten Höhe der Schleifwalze ab. Meine Schleifwalzen sind etwa 12,5 cm hoch, bei 25 mm Multiplex also 5 Scheiben. Sie werden mit Leim auf jeweils einer Oberfläche eingestrichen.
Jetzt steckst du die Scheiben auf eine Gewindestange mit dem Durchmesser des Zentrierbohrers der Lochsäge und presst sie mit jeweils einer Mutter und großen Unterlegscheiben zusammen, bis der Leim abgebunden hat.
Die so entstandene Walze spannst du in die Standbohrmaschine. Um die Oberfläche plan zu machen, klebst du mit Sprühkleber oder Leim ein halbes Blatt Schleifpapier (Körnung 80) auf ein glattes Brett. Wenn du nun die Bohrmaschine startest, kannst du das Schleifpapier langsam an die Außenseite der Walze halten und die Oberfläche solange bearbeiten, bis sie glatt und gleichmäßig ist.
Im Anschluss sägst du mit einer Bügelsäge oder einem Fuchsschwanz vorsichtig einen etwa 1 cm tiefen Schlitz längs in die Rolle.
Das ist beim ersten Mal etwas Fummelkram, aber es geht. Damit das Schleifpapier im Betrieb nicht herausrutschen kann, steckst du oben und unten in den Schlitz jeweils einen Nagel hinein und sicherst es damit. Fertig ist deine Schleifwalze, die du nun in unterschiedlichen Größen herstellen kannst. Das Prinzip bleibt immer gleich.
Nun entsteht beim Schleifen mit so einer Schleifwalze viel Schleifstaub. Außerdem ist es günstiger, wenn man eine Auflagefläche nutzen kann, die im rechten Winkel zum Schleifkörper steht. Dafür bauen wir uns nun einen Arbeitstisch mit Anschlussmöglichkeit für deinen Werkstattsauger.
Es handelt sich um einen etwa 10 cm hohen geschlossenen Kasten, in dem die Schleifwalze eintaucht. Durch ein Loch (35 mm Durchmesser) an der Seite wird der Staub abgesaugt.
Mir ist im Heimwerkeralltag sehr wichtig, dass der Aufbau immer schnell geht. Darum ist der Kasten so konstruiert, dass er auf meinen vorhandenen Bohrtisch mit Schraubzwingen befestigt werden kann.
Die Grund‐ und die Deckplatte sind genauso groß, wie der Bohrtisch: 700 mm breit und 250 mm tief. Der Kasten, in den die Schleifwalze eintaucht, muss nicht so groß sein (300x250 mm).
Da ich Schleifwalzen in unterschiedlichen Größen habe, muss das Loch der jeweiligen Größe entsprechen. Das geht am besten mit Einsätzen, die man austauschen kann. Dazu habe ich mit der Akkustichsäge einen viereckigen Ausschnitt (150x150 mm) ausgesägt und zwei Flacheisen mit einem Überstand unten angeschraubt. Darauf kann ich nun die Einsätze legen, die ich aus der gleichen Platte wie die Deckplatte hergestellt habe. So stelle ich sicher, dass alles plan ist. Für den Einsatz sägst du eine 150x150 mm große Platte zurecht. Das Loch in den Einsätzen sollte einen etwa 2 bis 3 mm größeren Durchmesser aufweisen, als die jeweilige Schleifwalze. Ich habe die Oberfläche der Einsätze mit meinem Multischleifer bearbeitet, damit sie ordentlich sitzen und das Werkstück nirgendwo hängen bleibt. An den Seiten kannst du für die Aufbewahrung der unterschiedlichen Einsätze noch eine lange Schraube eindrehen. Zum Schluss habe ich die Oberflächen der Deckplatte und der Einsätze mit Wachs behandelt (z. B. Antikwachs), damit sich das Werkstück besser führen lässt.
Fertig ist dein Arbeitstisch und somit der Spindelschleifer!